Precision Perfected: Unveiling the Power of Advanced Stator Winding Equipment Technology
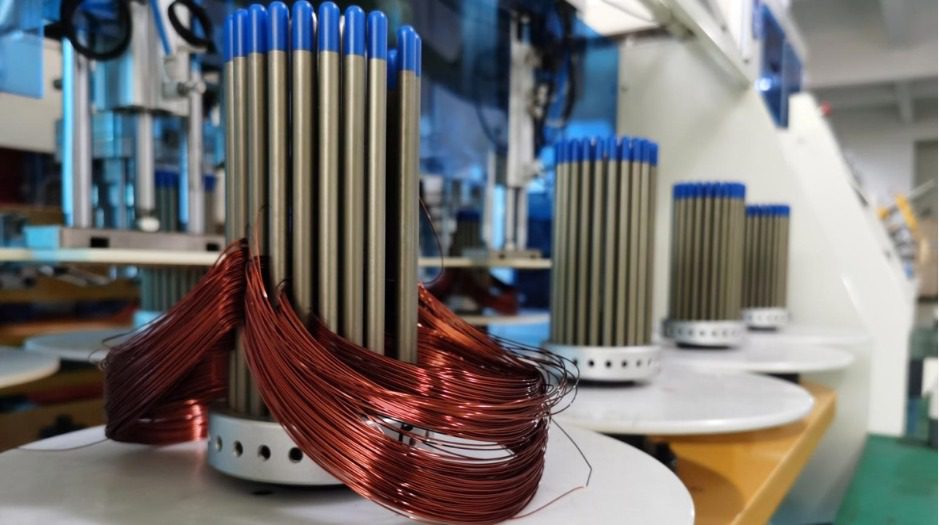
Introduction
In the intricate world of electrical engineering, precision is paramount. As technology continues to advance, the demand for more efficient and accurate stator winding equipment rises. In this article, we delve into the transformative power of cutting-edge stator winding technology and its role in revolutionizing stator production lines.
Understanding Stator Winding Equipment
Before we explore the advancements in stator winding equipment, it’s crucial to understand its fundamental role. Stator winding equipment forms the backbone of electrical machinery, facilitating the creation of intricate coil windings essential for generating electromagnetic fields within motors and generators. These coils are meticulously wound around the stator core, dictating the performance and efficiency of the electrical apparatus.
Over the years, stator winding technology has undergone a remarkable evolution. Traditional winding methods, while effective, often lacked the precision demanded by modern applications. However, with the advent of advanced automation and robotics, manufacturers can now achieve unparalleled levels of accuracy and efficiency in stator production.
Precision at its Core: Advanced Automation
At the heart of modern stator winding equipment lies advanced automation. Gone are the days of manual winding, replaced by sophisticated machinery capable of intricate coil formations with micron-level precision. By harnessing the power of robotics and computer-controlled systems, manufacturers can achieve uniform winding patterns and optimal wire tension, resulting in enhanced performance and reliability.
Optimizing Efficiency Through Robotics
One of the most significant advancements in stator winding technology is the integration of robotics into the production line. Robotic arms equipped with specialized end-effectors can swiftly and precisely wind coils around stator cores, reducing production time and minimizing human error. This seamless collaboration between man and machine ensures consistent quality while maximizing efficiency in stator production lines.
The Role of AI in Stator Winding Precision
Artificial Intelligence (AI) is revolutionizing stator winding technology by offering predictive capabilities and adaptive control systems. Through machine learning algorithms, AI can analyze vast amounts of data in real-time, optimizing winding parameters for maximum performance. By continuously refining its algorithms based on feedback from production processes, AI-driven stator winding equipment can adapt to varying conditions, further enhancing precision and efficiency.
Pushing Boundaries with IoT Integration
The Internet of Things (IoT) is seamlessly integrating stator winding equipment into interconnected production ecosystems. By equipping machinery with sensors and connectivity capabilities, manufacturers can monitor performance metrics in real-time and preemptively identify potential issues. This proactive approach to maintenance not only minimizes downtime but also ensures optimal performance throughout the stator production line.
Empowering the Future of Electrical Engineering
As we look ahead, the future of stator winding technology appears promising. Innovations in materials science, coupled with advancements in automation and AI, will continue to push the boundaries of precision and efficiency. With stator winding machine playing a pivotal role in powering various industries, from automotive to renewable energy, its evolution is set to shape the landscape of electrical engineering for years to come.
Conclusion
In conclusion, the advancement of stator winding equipment technology represents a significant leap forward in the quest for precision and efficiency in electrical engineering. Through the integration of advanced automation, robotics, AI, and IoT, manufacturers can achieve unparalleled levels of accuracy and productivity in stator production lines. As we embrace these innovations, we pave the way for a future where precision is not just a goal but a standard in electrical machinery manufacturing.